Обсудив в прошлой статье историю управления сборочной линией и балансировки линии, в этой статье мы рассмотрим 3 основных принципа эффективного управления линией и непрерывного потока на производстве и/или сборочной линии. К ним относятся;
- Поток процессов
- Поток материалов
- Поток информации
Эти три элемента собираются под тремя основными заголовками:
Обычно на линии сборки улучшается поток процессов только путем балансировки линии. Поток процессов является одним из трех основных элементов, улучшающих эффективность управления линией; однако невозможно говорить о здоровом и эффективном управлении линией без двух других ключевых элементов. Теперь давайте подробно рассмотрим эти три основных аспекта.
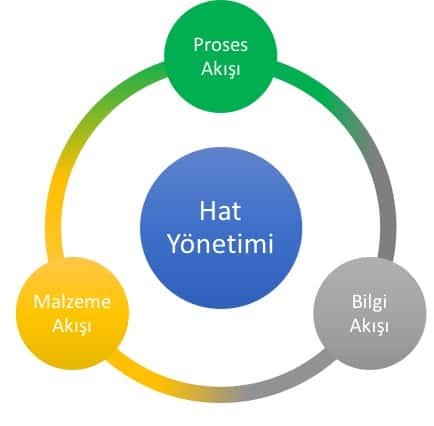
Поток процессов (производство)
Чтобы обеспечить здоровый поток на линии сборки, сначала необходимо изучить ёмкости и скорости производства процессов как по запросу клиента, так и внутренние.
Вы можете определить, достаточен ли ваш поток процессов, задав себе следующие вопросы:
- Высокий ли уровень запасов между процессами? Материалы ждут операторов или машин?
- Высокий ли уровень готовой продукции на складе? Переполнены ли вашими отгрузочными складами ненужные продукты?
- Можете ли вы точно измерить производительность и доступность ваших производственных линий?
- У вашего производства есть ритм? Или вы постоянно боретесь с переработкой?
Согласно принципу «Именно вовремя», производство в соответствии с потребностями клиента означает, что время цикла линии совпадает с тактовым временем (скоростью потребности клиента). Если время цикла короче, чем тактовое время, возникают потери из-за ранней избыточной продукции. Наоборот, если производство происходит позже тактового времени, возникает риск не выполнения заказов.
Поэтому необходимо правильно рассчитать тактовое время. Нужно учитывать не только тактовое время, но и общую ёмкость, чтобы определить, сколько ёмкости занимают другие группы продуктов, которые также должны быть произведены на линии. В противном случае, даже если расчёт тактового времени правильный, он не будет реалистичным из-за игнорирования ёмкости.
Так же как важно согласование производственной линии с темпом клиента, так же важно учитывать согласование между процессами или станциями внутри производственной линии. Даже если у процессов разные ёмкости, если их скорости производства не сбалансированы, не может быть обеспечен непрерывный поток в производстве. На линиях, где производство ведется без непрерывного потока, наблюдаются полуфабрикаты (Work In Process — WIP) между процессами.
На линии сборки ожидается, что общая продолжительность работы станций будет равна или меньше времени цикла. Поскольку все станции работают одновременно на линии сборки, ёмкость обычно общая для одной и той же группы продуктов. Поэтому, если ёмкость линии сборки рассчитана, нет необходимости рассчитывать ёмкость каждой станции отдельно. Скорость линии сборки равна скорости самой медленной станции, «узкое место«.
Однако эта ситуация не действительна для производственных линий за пределами линии сборки. Каждый процесс, разделяемый разными продуктами в плане ёмкости, может производить в разное время. В этом случае нельзя говорить о непрерывном потоке; однако для ускорения потока процессов необходимо применять правильные методы управления производством (FIFO, CONWIP, Канбан, Последовательное Потягивание), хотя и не настолько, как на линии сборки, чтобы управлять межпроцессными запасами и уменьшать партии.
Поток материалов
Процессный поток может быть идеально спроектирован, но если у производственной или сборочной линии нет сырья или полуфабриката, невозможно говорить о потоке на этой линии. Даже если автомобиль Формулы-1 безупречно проходит по трассе (производство), если он слишком долго ждет заполнения топливом или замены шин (поток материалов) во время остановки на боксах, он проиграет гонку. Потому что гонки Формулы-1 выигрываются как на трассе, так и в боксах.
Существует ли самый простой способ обеспечить безупречный поток материалов — создать непрерывную линию с непрерывным поступлением всех полуфабрикатов и сырья на ее стороне? Если у вас есть неограниченное пространство, деньги и терпение для борьбы с потенциальными дефектами качества, этот метод может показаться практичным, но он совершенно не экономичен.
Вы можете проанализировать, достаточен ли ваш поток материалов, задав себе следующие вопросы:
- Останавливают ли производство или операторы линию из-за ожидания материалов?
- Есть ли у ваших транспортных операций стандарт или транспортные элементы поставляют материалы только по заказу и количеству, как ученик в магазине?
- Есть ли у вас остановки для ящиков? Теряют ли операторы время из-за потерь при перевозке и обработке?
- Можно ли сразу найти необходимый материал на складе? Каков ваш уровень 5S?
При эффективном управлении линией материалы должны производиться партиями нужного размера, упаковываться в ящики в нужном количестве и передаваться в соответствующие места с нужной частотой и по нужному маршруту. Для этого необходимо четко определить стандарты, не только для контроля производства, но и для контроля потока материалов. Системы милкран можно управлять только с помощью здоровой схемы потока материалов. Значимость темы 5S будет еще более ощутима при обеспечении потока материалов.
Чтобы производить в правильных количествах, необходимо проанализировать мощности и использовать правильные методы контроля производства, как мы упоминали в разделе потока процессов.
Также необходимо правильно организовать методы укладки материалов от процесса поставщика к процессу потребителю или сборочной линии. Согласование партии, произведенной процессом поставщика, с скоростью потребления процессом потребителя столь же критично, как и укладка материалов в правильные ящики и стандартные количества. Всю базовую информацию, такую как определение количеств внутри ящиков с помощью планового подхода (PFEP) и стандартизация размеров типов ящиков, следует создавать на материальной основе.
Очень важно исследовать единицу, которая обеспечит поток материалов для правильного маршрута. Отходы транспортной команды должны быть исследованы, должна быть следована последовательность работы, и мощности должны быть проанализированы. Для транспортной команды должен быть установлен стандартный маршрут, и должна быть определена политика управления запасами в точках, где будет осуществляться поставка материалов. (Фиксированный цикл — переменный запас, фиксированный запас — переменный цикл)
Поток информации
Если вы организуете поток производства и корректно проектируете поток материалов, но все еще не можете обеспечить полностью поток информации, к сожалению, все еще невозможно поддерживать производственный процесс здоровым.
Вы можете проанализировать, достаточен ли ваш поток информации, задав себе следующие вопросы:
Можете ли вы мгновенно получить информацию о том, почему план производства не соблюдается, или это занимает до конца дня, чтобы понять ситуацию?
- Можете ли вы сразу выяснить, почему производственный план не может быть выполнен, или вам требуется время до конца дня, чтобы осознать ситуацию?
- Вы сталкиваетесь с проблемами качества из-за неправильной информации или неправильного понимания правильной информации?
- Производство как-то управляет проблемами, и поэтому вы постоянно обновляете свой производственный план?
- Можете ли вы проанализировать причины остановок линии, или ваши производственные проблемы испаряются?
- Вы постоянно обновляете свой производственный план и несколько раз пересматриваете обновленный план в конце дня?
Чтобы обеспечить корректный поток информации, необходимо облегчить доступ к информации в производстве, создать системы, которые будут контролировать поток информации в производстве и создавать качество во время производства (доски канбан, визуализация супермаркетов, андоны, системы пока йок), создать культуру производства, которая выявит проблемы, и предпринять предупредительные действия по их перманентному устранению через ежедневные управленческие совещания.
В противном случае, с окружением производства, где вы ничего не можете сделать, кроме как постоянно пересматривать производственные планы из-за недостатка потока информации, вы столкнетесь с дефектами качества, которые могут возникнуть из-за недостатка потока информации, и возобновленных пожаров.