После первой промышленной революции, начавшей массовое производство с паровыми машинами (Индустрия 1.0), логика массового производства, направленная на увеличение производительности работников путем разбиения задач на маленькие части, как это делал Генри Форд, принесла вторую промышленную революцию (Индустрия 2.0). Концепция балансировки линии возникла именно отсюда.
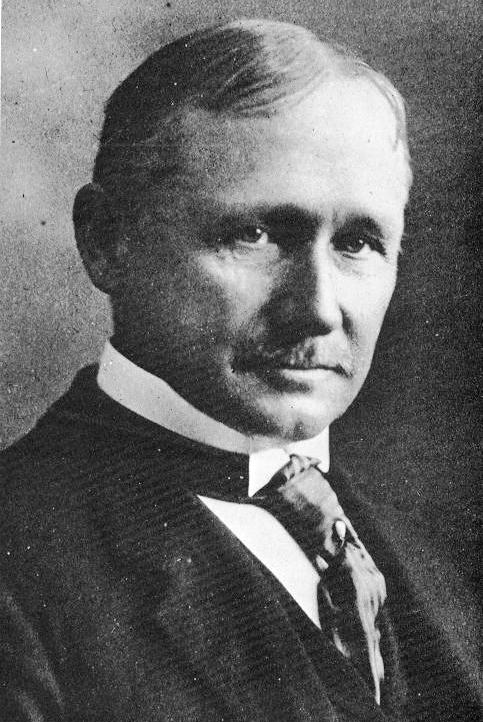
Принципы улучшения производительности работников, описанные со всеми деталями в книге Фредерика Уинслоу Тейлора «Принципы научного управления», заложили основу для промышленной инженерии и линейного управления.
Разбивая задачи на самые простые компоненты и равномерно распределяя их между работниками для минимизации мастерства, а также максимизации скорости производства через повторяющиеся задачи, этот метод стал отправной точкой для балансировки линии и Индустрии 2.0.
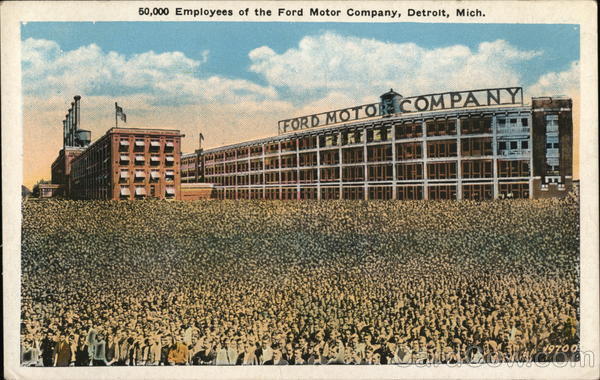
Через эти линии сборки, где Генри Форд сократил время производства на более чем 80% в своей знаменитой фабрике в Детройте, автомобиль перестал быть товаром, который мог позволить себе только аристократ, и стал мечтой для всех. Таким образом, с трансформацией транспорта и логистики начали формироваться современные жизни и города. Это привело к появлению так называемого фордизма, который стал предметом для книг по социологии.
От Однообразных Моделей к Разнообразным Товарам
Одним из самых больших недостатков на фабрике Форда было обеспечение серийности в производстве через производство автомобилей одного цвета и типа. Эта ситуация была подтверждением знаменитой фразы Генри Форда: «Вы можете получить машину любого цвета у меня, лишь бы она была черной.» Позднее, с появлением на рынке General Motors, появилось разнообразие продуктов-моделей-цветов. С 1930-х годов в игру вступила и Европа, и автомобили, включая те, что от Форда, начали разнообразиться и окраситься по модели и цвету.
Однако Форд начал отставать от General Motors, потому что, помимо достижения простоты путем разбиения задач на маленькие части, он не смог полностью развить свои организационные навыки.
Управление Продуктовым Разнообразием с Ограниченными Ресурсами
В то время как все это происходило в Америке и Европе, японцам пришлось производить по-другому, чем существующие методы производства. После Второй мировой войны им пришлось использовать ограниченные японские ресурсы (оборудование, материалы и т. д.) не только для превращения производства в серийное, но и для производства автомобилей на ограниченной территории Японии и конкуренции с Европой и Америкой путем создания конкурентоспособных продуктов.
Для этого им нужны были различные способы обеспечения разнообразия продукции. С помощью разработанной ими техники SMED они смогли сократить временные затраты на смену формы, которые составляли 1 день, до менее 10 минут, увеличивая тем самым производительность и делая возможным производство различных продуктов на одном и том же оборудовании.
Позвольте им Производить!
Еще одно, что японцы делали по-другому, — это «культурные искажения» в логике производства на линиях сборки. Массовое производство должно быть «массовым», как и следует из названия, и линия сборки никогда не должна останавливаться. Даже если возникают ошибки качества, производство должно продолжаться, и эти ошибки должны быть исправлены в зоне ремонта, а затем объем производства должен быть сохранен любой ценой.
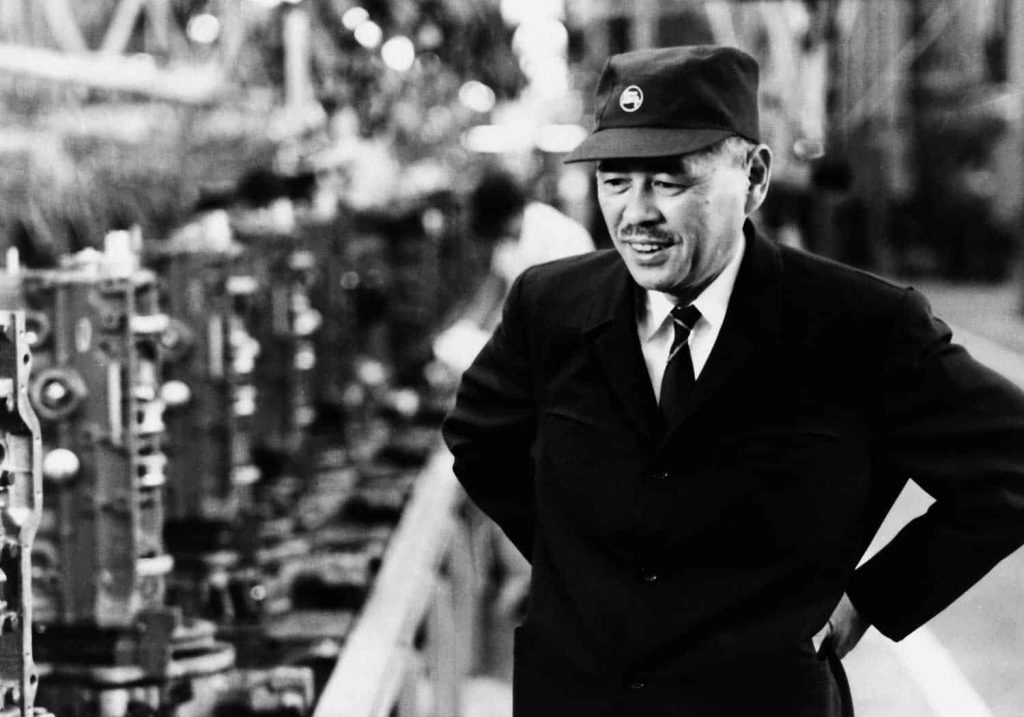
Однако здесь была упущена важная деталь, которую заметил Тайити Оно. Даже если возникают ошибки качества, логика «позвольте им производить!» приводила к множеству потерь из-за повтор Невозможно, чтобы каждая деталь, собираемая во все более сложных автомобилях, проходила контроль качества в конце линии. Автомобили, которые проверялись по ограниченным пунктам и исправлялись «относительно» при наличии каких-либо дефектов или недостатков, в глазах клиента были потенциальным источником возможных проблем с качеством.
Качество на месте (в процессе производства)
Когда Охно изучил линии, он понял, что дефект, который можно было легко устранить во время сборки, требует больше времени (и более высокой оплаты сверхурочных) для устранения на ремонтных линиях, просто потому, что сборка задерживается, чтобы можно было продолжить сборку. Эти ремонты были чисто противопожарными, корректирующими мероприятиями, которые решали проблему поверхностно, не добираясь до первопричины. Это означало, что один и тот же дефект качества повторялся снова и снова, а время ремонта исчислялось многими часами потерянного времени.
Отправной точкой концепции Built In Quality (или Quality While Producing), о которой мы сегодня очень часто говорим, является устранение отходов ремонта-коррекции-ремонта на классических сборочных линиях. Поначалу такой подход может восприниматься как чрезмерная остановка сборочных линий; однако по мере устранения проблем вместе с их первопричинами закладывается фундамент сборочной линии, которая никогда больше не остановится из-за одной и той же проблемы.
Кто лучше всех разбирается в бизнесе?
Еще одна примечательная особенность сборочных линий типа Toyota заключалась в том, что первая инициатива по решению проблем с качеством всегда была на стороне оператора. Тейлор и Форд в своих сборочных линиях операторы были ресурсами, ответственными за обеспечение работы линий с физической силой и должны были работать на них непрерывно, не прекращая производство. Поэтому, поскольку проблемы качества были «вещами», которые нужно было решать позже, операторы никогда не беспокоились о том, чтобы решать проблемы или улучшать линию.
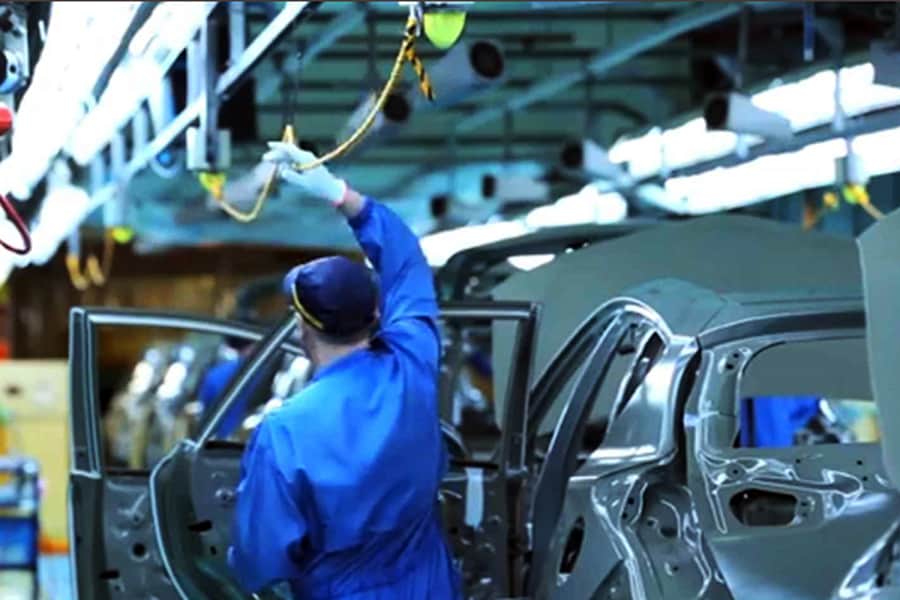
В линиях, спроектированных Оно, однако, операторы были первыми лицами, ответственными за качество, и столкнувшись с любой проблемой качества, они имели право остановить линию, потянув за шнур Andon. Они не были нанятыми мышцами, просто чтобы поддерживать производство, а скорее сотрудниками, ответственными за качество и эффективность с их идеями и предложениями. Потому что по мнению Оно, «Качество не контролируется, оно встроено в процесс!» Линии сборки, где возникло восприятие «Тот, кто лучше всего делает работу, знает лучше», формируют основу как для фундаментальной ценности «Уважение к людям» в Toyota Way, так и для Jidoka, одного из основных принципов TPS.
Лидерство и Управление Линией
Еще одним значимым аспектом, отличающимся Lean сборочные линии от классических сборочных линий, является концепция лидерства на линии. Классические сборочные линии были спроектированы на основе принципа непрерывной работы, где работников плавно пацили с помощью определенной скорости конвейера. Рабочим необходимо было быть наполненными задачами таким образом, чтобы они не думали как можно больше, повторяя одну и ту же задачу как можно быстрее и стандартизированно.
Придуманная Оно концепция Встроенного Качества приняла идею выявления и устранения ошибок качества во время производства, поэтому она также представила концепцию Лидера Линии, ответственного за вмешательство в возникающие проблемы и общий «порядок» на линии. Лидеры линии были в должности руководителей групп из 5-7 человек на сборочной линии, полностью ответственными за все выполняемые задачи, за производительность и качество линии, а также оказывали поддержку членам команды на линии в случае их отсутствия и колебаний в производительности. Помимо требования к сильным навыкам решения проблем, эти лидеры были гораздо более чем мышцы, описанные Тейлором в 1910-х годах. Они были не просто операторами, а скорее менеджерами, ответственными за результативность их линейного участка.
Учитывая, что до сих пор многие заводы имеют команды из 50-80-100 человек обычно под одним сменным супервайзером, несложно сказать, что этот метод является частью достаточно иерархической и систематической структуры. Мы рассмотрим детали этой структуры позже.
Продолжение в Следующей Статье
В этой статье мы рассмотрели краткую историю сборочных линий и концепции, приводящие от классических сборочных линий к Линиям Линии и Управлению Линией. В следующей статье мы продолжим с основными принципами балансировки линии в сборочной линии.
Если вы хотите получить более подробную информацию по этому вопросу и изучить линейное управление балансировкой на практике здесь Вы можете зарегистрироваться на тренинг Ямазуми, нажав здесь.
Ссылки
- Тейлор, Ф. У., Принципы научного управления, 1911 г.
- Оно, Т., Производственная Система Toyota: За рамками крупномасштабного производства, 1988 г.
- Джонс, Д. Т., Уомак Дж., Lean Thinking: Избавьтесь от потерь и создайте богатство в вашей корпорации, 1996 г.
- Toyota Motor Corporation, Toyota Way 2001, 2001 г.